Apa itu Process Flow Diagram?
Process Flow Diagram (PFD) adalah jenis diagram alir yang menggambarkan hubungan antara komponen utama di pabrik industri. PFD paling sering digunakan dalam teknik kimia dan teknik proses, meskipun konsepnya kadang-kadang diterapkan pada proses lainnya. Diagram ini digunakan untuk mendokumentasikan suatu proses, meningkatkan proses, atau memodelkan proses baru. Tergantung pada penggunaan dan isinya, PFD juga dapat disebut sebagai Process Flow Chart, Flowsheet, Block Flow Diagram, Schematic Flow Diagram, Macro Flowchart, Top-down Flowchart, Piping and Instrument Diagram, System Flow Diagram, atau System Diagram.
Dalam PFD, digunakan serangkaian simbol dan notasi untuk menggambarkan suatu proses. Simbol-simbol ini bervariasi di berbagai tempat, dan diagramnya dapat berkisar dari coretan tangan sederhana atau catatan tempel hingga diagram yang terlihat profesional dengan detail yang dapat diperluas, yang dibuat dengan perangkat lunak.
Sejarah Process Flow Diagram (PFD)
Process Flow Diagram (PFD) memiliki sejarah panjang yang berakar dari kebutuhan industri untuk mengoptimalkan dan mengontrol proses produksi. Pada awal abad ke-20, industri mulai berkembang pesat dan kompleksitas proses produksi meningkat. Hal ini mendorong para insinyur untuk mencari cara yang lebih efektif dalam memahami dan mengelola proses tersebut.
Awal Penggunaan PFD
Pada tahun 1920-an dan 1930-an, diagram alir sederhana mulai digunakan dalam industri kimia dan manufaktur. Pada masa ini, PFD digunakan untuk menggambarkan alur proses secara keseluruhan, memungkinkan insinyur dan manajer untuk melihat hubungan antara berbagai komponen dalam sistem produksi.
Perkembangan di Era Perang Dunia II
Selama Perang Dunia II, kebutuhan akan produksi massal dan efisiensi yang lebih tinggi mendorong pengembangan lebih lanjut dari PFD. Insinyur mulai menggunakan diagram ini untuk merancang pabrik yang lebih efisien dan untuk memastikan bahwa proses produksi dapat berjalan dengan lancar tanpa hambatan. Penggunaan PFD membantu dalam mengidentifikasi titik-titik lemah dalam proses produksi dan memungkinkan perbaikan yang cepat dan efektif.
Peningkatan Teknik dan Standarisasi
Pada tahun 1950-an dan 1960-an, penggunaan PFD semakin meluas dengan perkembangan teknik dan alat baru. Standarisasi simbol dan notasi untuk PFD mulai diperkenalkan, yang membuatnya lebih mudah dipahami dan diterapkan di berbagai industri. Organisasi seperti American National Standards Institute (ANSI) dan International Organization for Standardization (ISO) memainkan peran penting dalam standarisasi ini.
Era Digital dan Perangkat Lunak
Dengan munculnya teknologi komputer pada tahun 1970-an dan 1980-an, pembuatan PFD menjadi lebih mudah dan akurat. Perangkat lunak khusus untuk membuat PFD dikembangkan, memungkinkan insinyur untuk membuat diagram yang lebih kompleks dan detail dengan lebih efisien. Perangkat lunak ini juga memungkinkan untuk simulasi proses, yang membantu dalam perencanaan dan pengujian sebelum implementasi nyata.
PFD dalam Industri Modern
Di era modern, PFD digunakan secara luas di berbagai industri seperti kimia, minyak dan gas, makanan dan minuman, farmasi, dan banyak lagi. PFD menjadi alat penting dalam manajemen proyek, pengendalian mutu, dan pelatihan karyawan. Integrasi dengan teknologi digital dan Internet of Things (IoT) juga memberikan peluang baru untuk mengoptimalkan proses produksi secara real-time.
Tujuan dan Manfaat Process Flow Diagram (PFD)
Process Flow Diagram (PFD) memiliki berbagai tujuan dan manfaat yang penting dalam industri. Berikut ini beberapa tujuan utama dan manfaat dari penggunaan PFD:
1. Mendokumentasikan Proses
PFD digunakan untuk mendokumentasikan suatu proses guna memberikan pemahaman yang lebih baik, kontrol kualitas, dan pelatihan karyawan. Dengan PFD, setiap langkah dalam proses dapat dilihat secara visual, memudahkan pemahaman bagi semua pihak yang terlibat.
2. Standarisasi Proses
PFD membantu dalam standarisasi proses untuk mencapai efisiensi optimal dan keterulangan. Dengan standar yang jelas, proses dapat dijalankan dengan konsisten, mengurangi kesalahan, dan meningkatkan produktivitas.
3. Menganalisis Efisiensi Proses
PFD digunakan untuk mempelajari efisiensi dan peningkatan proses. Diagram ini membantu dalam mengidentifikasi langkah-langkah yang tidak perlu, hambatan, dan ketidakefisienan lainnya. Dengan analisis ini, perusahaan dapat melakukan perbaikan yang diperlukan.
4. Memodelkan Proses Baru
PFD digunakan untuk memodelkan proses yang lebih baik atau menciptakan proses baru. Dengan diagram ini, perusahaan dapat merancang alur kerja yang lebih efisien dan efektif sebelum implementasi di lapangan.
5. Komunikasi dan Kolaborasi
PFD memfasilitasi komunikasi dan kolaborasi dengan menyediakan diagram yang mudah dipahami oleh berbagai peran dalam organisasi atau di luar organisasi. Dengan PFD, semua pihak dapat memiliki gambaran yang sama mengenai proses yang sedang dijalankan.
Kesimpulan
Process Flow Diagram adalah alat yang sangat berguna dalam berbagai aspek manajemen proses. Mulai dari mendokumentasikan hingga meningkatkan efisiensi, PFD membantu perusahaan dalam mencapai tujuan mereka dengan lebih efektif. Semoga informasi ini membantu Anda memahami pentingnya PFD dalam industri.
Simbol dan Elemen dalam Process Flow Diagram (PFD)
Simbol PFD yang paling umum digunakan saat ini berasal dari berbagai lembaga seperti International Organization for Standardization (ISO 10628 – Flow Diagrams for Process Plants, General Rules), German Institute for Standardization (DIN), dan American National Standards Institute (ANSI). Namun, banyak perusahaan menggunakan simbol mereka sendiri yang sering kali serupa tetapi bisa berbeda dalam detailnya.
Anda dapat menemukan daftar lengkap simbol standar dengan panduan simbol PFD kami.
Elemen-elemen yang Biasanya Ada dalam PFD untuk Proses Tunggal:
Peralatan Utama:
Mencakup nama dan nomor ID. Contohnya termasuk kompresor, mixer, vessel, pompa, boiler, dan pendingin.
Pipa Proses:
Memindahkan produk, biasanya cairan, antar peralatan.
Arah Aliran Proses
Katup Kontrol dan Katup Penting Proses
Sistem Bypass dan Resirkulasi Utama
Data Operasional:
Seperti tekanan, suhu, densitas, laju aliran massa, dan keseimbangan massa-energi. Nilai-nilai ini sering mencakup minimum, normal, dan maksimum.
Komposisi Cairan
Nama Aliran Proses
Koneksi dengan Sistem Lain
Elemen yang Biasanya Dikecualikan dalam PFD:
Kelas Pipa dan Nomor Jalur Pipa
Instrumen Kontrol Proses
Nilai Bypass Minor
Katup Isolasi dan Shutoff
Ventilasi dan Drainase Pemeliharaan
Katup Relief dan Katup Keamanan
Informasi Kelas Kode
Jenis-Jenis Lain dari Process Flow Diagram (PFD)
Ketika diagram perlu menunjukkan beberapa proses unit di pabrik, diagram tersebut menjadi lebih seperti gambaran umum yang mengandung lebih sedikit detail. Diagram ini juga disebut Block Flow Diagram dan Schematic Flow Diagram. Setiap blok dapat menggambarkan satu peralatan atau tahap dalam suatu proses. Sebuah persegi panjang biasanya digunakan untuk menunjukkan peralatan dan label mengilustrasikan fungsinya. Aliran proses biasanya ditunjukkan dari kiri ke kanan, dan panah menunjukkan arah aliran.
Block Flow Diagram (BFD) dan Schematic Flow Diagram (SFD)
Block Flow Diagram (BFD) dan Schematic Flow Diagram (SFD) digunakan untuk memberikan gambaran umum tentang proses dengan fokus pada tahap utama atau peralatan. Mereka kurang detail dibandingkan dengan PFD tetapi berguna untuk memberikan pemahaman cepat tentang aliran proses keseluruhan di pabrik.
Piping and Instrument Diagram (P&ID)
Di sisi lain, Piping and Instrument Diagram (P&ID) lebih teknis, menggambarkan detail mekanis untuk perancang pipa, insinyur listrik, insinyur instrumen, dan ahli teknis lainnya yang memerlukan detail ini lebih daripada detail proses. P&ID mengambil aspek konseptual dari PFD dan menambahkan detail tentang peralatan, urutan proses, pipa proses dan utilitas, jalur bypass, instrumen, katup, ventilasi, drainase, dan item lainnya.
Kesimpulan
Memahami berbagai jenis Process Flow Diagram (PFD) sangat penting untuk berbagai tujuan dan kebutuhan teknis dalam industri. Block Flow Diagram dan Schematic Flow Diagram memberikan gambaran umum yang lebih sederhana, sementara Piping and Instrument Diagram memberikan detail teknis yang lebih mendalam. Dengan memilih jenis diagram yang tepat, perusahaan dapat meningkatkan efisiensi dan akurasi dalam desain dan operasi mereka.
Bagaimana Meneliti dan Merencanakan Process Flow
Meneliti dan merencanakan process flow memerlukan pendekatan yang sistematis dan detail. Berikut adalah langkah-langkah yang dapat Anda ikuti untuk memastikan diagram alur proses yang efektif dan akurat:
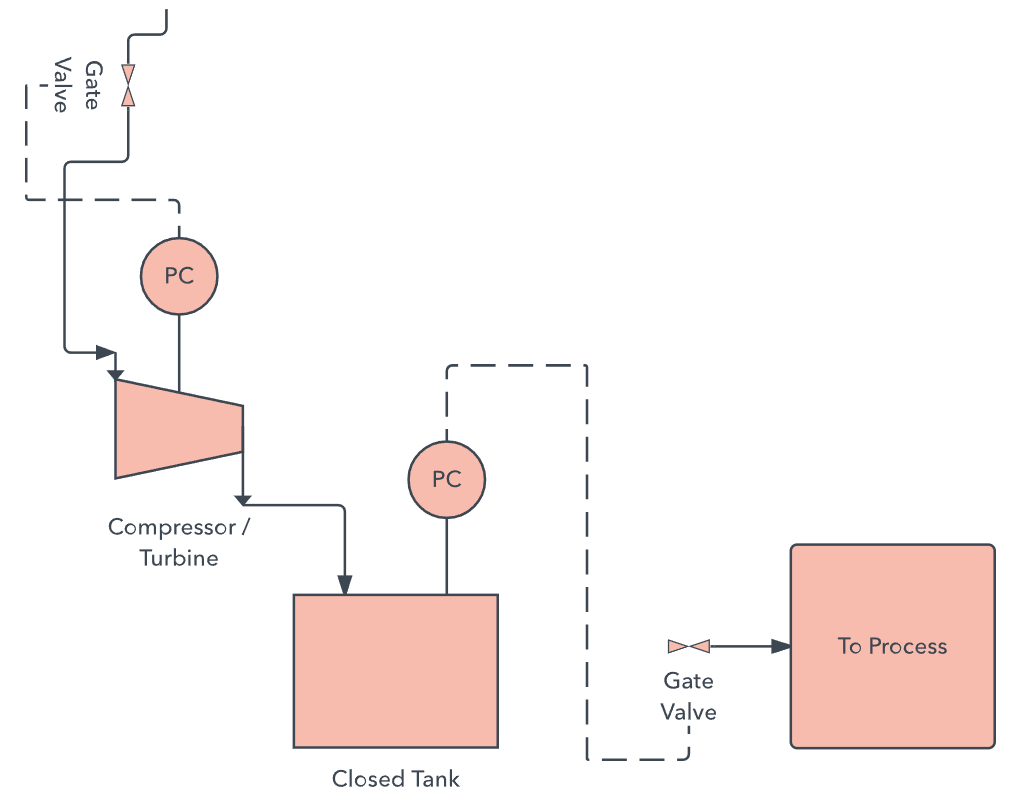
1. Tentukan Ruang Lingkup Proses
Definisikan ruang lingkup proses yang akan dipelajari dan apa yang ingin Anda capai. Identifikasi batasan-batasan proses dan tentukan tujuan penelitian, apakah untuk dokumentasi, peningkatan kualitas, atau tujuan lainnya.
2. Tentukan Tingkat Detail
Tentukan tingkat detail yang diperlukan untuk tujuan Anda. Untuk proses yang rumit, beberapa versi diagram mungkin perlu dibuat untuk berkomunikasi dengan orang-orang dalam peran yang berbeda. Misalnya, manajer mungkin memerlukan gambaran umum sementara teknisi memerlukan detail spesifik.
3. Lakukan Penelitian
Untuk proses yang kompleks seperti di pabrik industri, penelitian dapat dilakukan melalui tim proyek, kelompok kontrol kualitas, atau konsultan. Untuk proses yang lebih kecil dan sederhana, Anda mungkin bisa melakukannya sendiri, mungkin dengan memulai dari catatan tempel (sticky notes).
4. Pelajari Peralatan, Aktivitas, dan Hubungan
Pelajari peralatan, aktivitas, dan hubungan melalui observasi dan wawancara. Jika Anda sedang memodelkan proses baru, pelajari data yang tersedia, termasuk standar untuk produk yang dihasilkan dalam proses tersebut.
5. Gambar Diagram Draf
Buat diagram draf dan konfirmasikan dengan orang-orang yang terlibat dalam proses. Lakukan perubahan, penambahan, atau penghapusan yang diperlukan dengan kolaborasi mereka untuk memastikan akurasi dan kesesuaian dengan kenyataan di lapangan.
6. Gunakan Diagram untuk Tujuan yang Diharapkan
Setelah diagram selesai dan diverifikasi, gunakan untuk tujuan yang dimaksud, seperti dokumentasi, jaminan kualitas, perbaikan proses, atau tujuan lainnya. Diagram ini sekarang dapat menjadi alat yang berharga untuk mengoptimalkan dan mengelola proses secara efektif.